Building Solar Cars (2006-2010)
As an undergrad at Michigan, I spent my first 3.5 years as an active
member of the University of Michigan Solar Car Team, culminating with
racing Michigan's 10th car, Infinium, in Australia in the fall of 2009.The design principles for solar cars provided numerous challenges that often resulted in novel designs. In particular, the principles kept in mind were (1) reliability; (2) light weight; and (3) mechanical parts give as much freedom to the aerodynamic design as possible.
To follow the latest project/car, see UMSolar.com.
Continuum
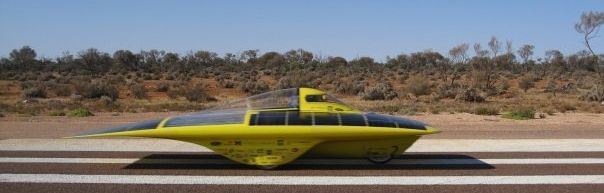
In 2006/2007 I started off learning the ropes by helping build the 9th car, Continuum. I designed the titanium roll-cage for that car, including doing FEA calculations, but more importantly learned to lay up carbon fiber, cut it, and similar hands-on tasks.
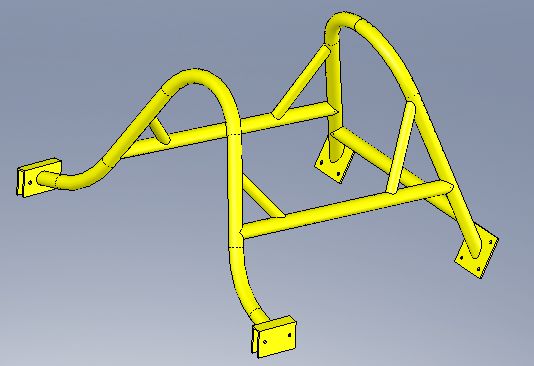
In 2007/2008 we built a mule car, but never finished... the idea of a mule-car being to test out features for the next car, sans aerobody. Few of the concepts turned out to be relevant, due to rule changes that resulted in the Infinium instead having a 2-front;1-back wheel configuration.
Infinium
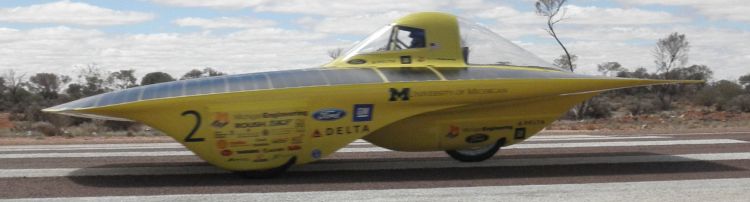
During 2008 and the first half of 2009 was when we designed and built Infinium. Most of the construction occurred in summer 2009, with the completed car being flown to Australia in September. The following month and a half in Australia were used for final improvements and testing.
The steering system initially attempted to implement the Peaucellier-Lipkin linkage as a weight saving alternative to a standard rack and pinion. A prototype assembly was made, but the final car used a rack and pinion, since reliability was more important. The nearly complete alternate design is shown below.
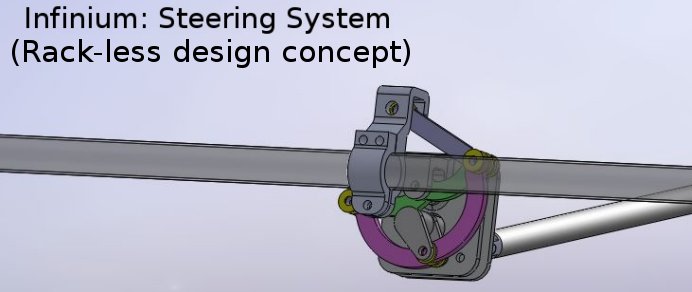
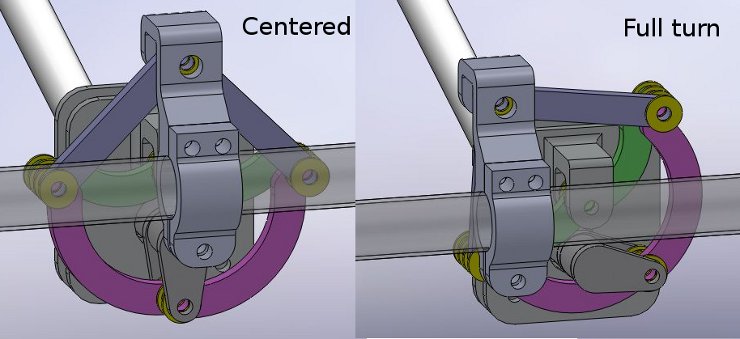
The final, rack and pinion-using design is shown below.
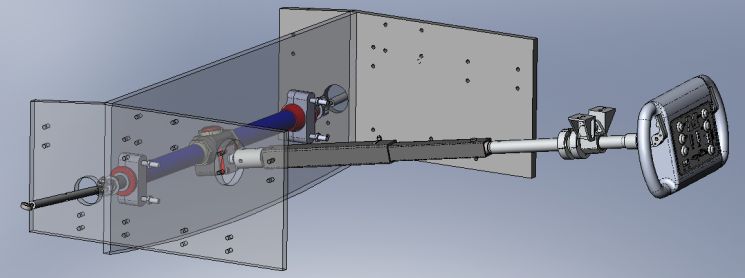
The steering wheel was made from two halves of carbon fiber with custom molds, and was designed to contain the electronics, be light weight, and ergonomic. A few iterations were done to improve build quality. Getting a good quality carbon layout in the hand-holds was the biggest trick. A single thumb-bolt provided easy access to the electronics (and four fake bolt heads were included for aesthetic value).
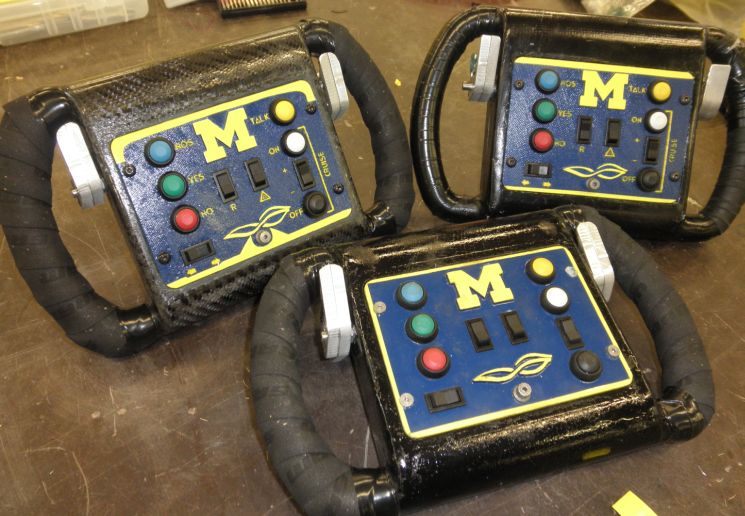
A collapsible steering column was deemed a worthwhile feature. However, cost and weight of COTS options made an in-house solution desirable. The final steering column used square aluminum tubing, with a thin-walled aluminum break-pin (groved aluminum arrow shafts, in fact). Static load testing was done to improve reliability. Testing also showed that the initial approach of using two weaker break-pins was far less reliable.
A pic from testing is below. Static loading of around 150 lbs is shown. All of this weight is carefully balanced on about a square inch of cross section, and of course, weights went rolling during each test.
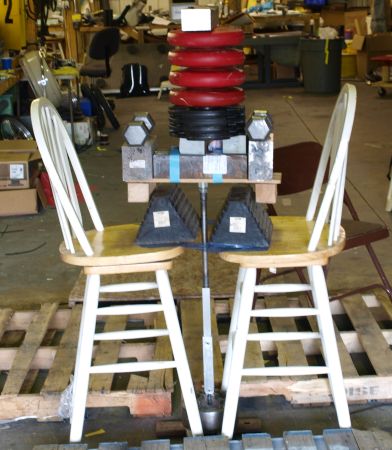
The driver's cockpit has a canopy that opens. In addition to weight, the canopy on the car's upper surface needs to be robust enough to be thrown open during emergency egreess, and stay open. Getting a good bond between metal parts and the carbon fiber canopy and upper surface proved to be the biggest issue, and general point of failure. Rods holding the canopy open, and limiting the amount of opening lock in place via gravity. Due to the fragile solar cells being used on Infinium, having redundancy trumped weight concerns.
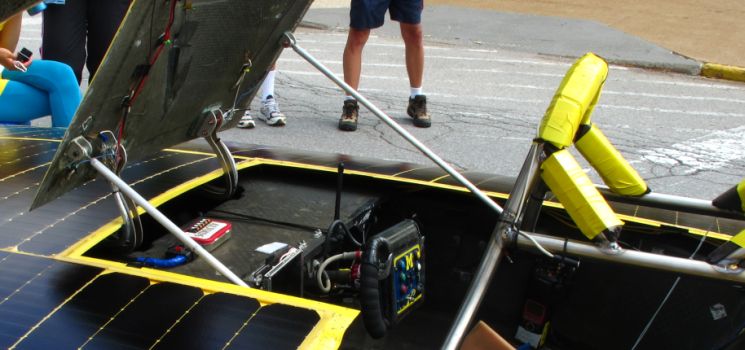
Finally, the array stand -- to hold the car at an angle when charging in the mornings and evenings -- was built primarily of square steel tubing, and the perforated square tubing used for sign posts.
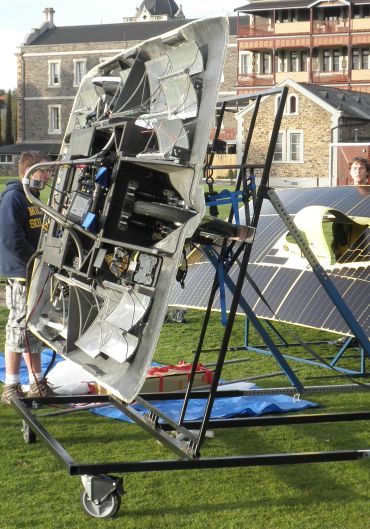
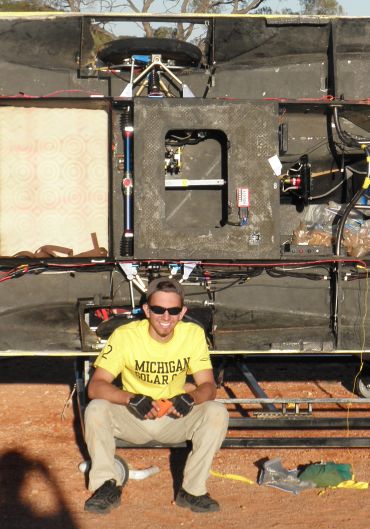
-1-28-13